再攀火箭固体动力新高峰
——记航天科技四院3.5米整体式固体火箭发动机研制团队
伴随着撼天动地的轰鸣,发动机喷出耀眼的“火龙”,“30秒,40秒,50秒……”,屏幕上画出一条完美的推力曲线,“成功了!”雷鸣般的掌声立刻在航天科技四院实验区视频大厅响起。10月19日,我国研制的世界推力最大的整体式固体火箭发动机地面热试车获得圆满成功。
从2米到3米、再到3.5米,从120吨到200吨、再到500吨,发动机直径和推力不断创造新的高度;从我国长征系列第一型全固体运载火箭,到首枚固液动力结合火箭立项研制,10多年时间,不断创造固体发动机研制奇迹的就是该院固体运载火箭发动机团队。
在自主创新中快速成长
中国航天一个很大的财富就是拥有一批有理想、有信念、有本领的航天青年,而航天科技四院固体运载动力团队正是这样一个朝气蓬勃的青年队伍。
2007年团队成立,第一批研究人员仅有7人;2010年,成立了固体运载动力技术研究室;2012年,国家正式将大推力固体火箭发动机立项,团队逐渐成长并得到扩充。
研制初期,经验空白,遇到的困难可想而知。这支团队翻阅几乎能查到的国内外所有资料,经过无数次探讨和试验,在国内率先成功研制了推力120吨、当时国内最大的整体式固体火箭发动机。
在总师王健儒的带领下,研制团队攻克一系列难关。从2005年的理论预研,到2015年长征十一号首飞成功,再到如今的直径3.5米整体式固体火箭发动机试车成功,王健儒也成了我国固体运载动力技术领域的领军人物之一。
王健儒被同事称为技术问题的“活字典”。“问一下王总,你就会清楚”,他总能第一时间调动大脑数据库的存储系统,迅速跟当下所面临的问题进行匹配,搜索出相关结果和数据。
很多人无法想象,“味道”是王健儒工作的关键词。“每次燃烧试验做完,就要第一时间爬进燃烧室,看绝热层烧蚀情况,仔细测出烧完后的剩余量,为后续研制积累数据。”他说,其实,闻到的都是各种碳化物、氯化物等化学物质的刺鼻气味。现在,绝热层燃烧前后味道的变化,他一闻便知。
“我们要敢于打破传统设计理念,勇于尝试全新设计方法和技术,做到设计与工艺融合,确保产品设计一次成功!”这是技术带头人白彦军的座右铭。
在型号研制过程中,白彦军带领团队做到了“能仿就仿”,最大限度采用仿真与试验相结合的手段获得一手数据来进行定量表征,让设计更有把握。
这支平均年龄不到35岁的年轻设计团队,已经相继攻克和掌握了全数字化总体设计与管理等多项技术,实现了固体动力在长征和捷龙系列运载火箭中的应用。
在攻坚克难中铸造一流发动机
“没有条件,我们就创造条件。”面对研制场地、设备能力均达到或者超过当时已有条件极限的情况,43所壳体技术负责人李瑞珍带领大家,拉开了一场挑战复合材料成型极限的“赛跑”。
研制期间,李瑞珍几乎每天都要去壳体生产现场。“壳体尺寸大幅增长,首要解决的就是芯模成型问题。”她说,原有的砂芯模重量大、挠度大,石膏芯模易开裂、产品表观质量差。
团队将目光聚焦到金属芯模上,10余种方案推翻重来,数百张图纸修改完善,最终应用镂空设计原理确定了金属芯模成型方案,保证了壳体顺利研制。
发动机研制生产完毕,即将接受最后一道考验地面试车,却遇到了一个棘手问题,如何突破吊车承载极限、吊高极限等,使之稳落于试验架?
这时,401所一室高永刚提出一个新想法,台体吊与汽车吊合力完成。然而,汽车吊工作路径为弧线、台体吊是“十”字,路径矛盾怎么解决、载重如何分配?当晚,团队立即投入推演路径设计、质心计算、支撑部位、吊具强度等工作中。
近200天里,他们经历了7次大型专家评审会,完成了重点承力部位的工装设计优化、强度和刚度校核,反复演练了起升高度、移动速率、各方位牵引力……
10月19日,伴随着巨大的振动与轰鸣,试验数据呈现出完美的测试曲线。而这成功的曲线,就是对团队人员辛勤付出最大的回报。
实习记者 李旭东
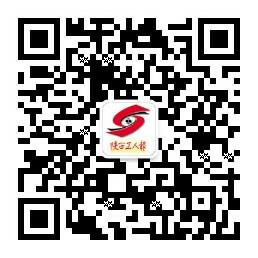
关注公众号,随时阅读陕西工人报
伴随着撼天动地的轰鸣,发动机喷出耀眼的“火龙”,“30秒,40秒,50秒……”,屏幕上画出一条完美的推力曲线,“成功了!”雷鸣般的掌声立刻在航天科技四院实验区视频大厅响起。10月19日,我国研制的世界推力最大的整体式固体火箭发动机地面热试车获得圆满成功。
从2米到3米、再到3.5米,从120吨到200吨、再到500吨,发动机直径和推力不断创造新的高度;从我国长征系列第一型全固体运载火箭,到首枚固液动力结合火箭立项研制,10多年时间,不断创造固体发动机研制奇迹的就是该院固体运载火箭发动机团队。
在自主创新中快速成长
中国航天一个很大的财富就是拥有一批有理想、有信念、有本领的航天青年,而航天科技四院固体运载动力团队正是这样一个朝气蓬勃的青年队伍。
2007年团队成立,第一批研究人员仅有7人;2010年,成立了固体运载动力技术研究室;2012年,国家正式将大推力固体火箭发动机立项,团队逐渐成长并得到扩充。
研制初期,经验空白,遇到的困难可想而知。这支团队翻阅几乎能查到的国内外所有资料,经过无数次探讨和试验,在国内率先成功研制了推力120吨、当时国内最大的整体式固体火箭发动机。
在总师王健儒的带领下,研制团队攻克一系列难关。从2005年的理论预研,到2015年长征十一号首飞成功,再到如今的直径3.5米整体式固体火箭发动机试车成功,王健儒也成了我国固体运载动力技术领域的领军人物之一。
王健儒被同事称为技术问题的“活字典”。“问一下王总,你就会清楚”,他总能第一时间调动大脑数据库的存储系统,迅速跟当下所面临的问题进行匹配,搜索出相关结果和数据。
很多人无法想象,“味道”是王健儒工作的关键词。“每次燃烧试验做完,就要第一时间爬进燃烧室,看绝热层烧蚀情况,仔细测出烧完后的剩余量,为后续研制积累数据。”他说,其实,闻到的都是各种碳化物、氯化物等化学物质的刺鼻气味。现在,绝热层燃烧前后味道的变化,他一闻便知。
“我们要敢于打破传统设计理念,勇于尝试全新设计方法和技术,做到设计与工艺融合,确保产品设计一次成功!”这是技术带头人白彦军的座右铭。
在型号研制过程中,白彦军带领团队做到了“能仿就仿”,最大限度采用仿真与试验相结合的手段获得一手数据来进行定量表征,让设计更有把握。
这支平均年龄不到35岁的年轻设计团队,已经相继攻克和掌握了全数字化总体设计与管理等多项技术,实现了固体动力在长征和捷龙系列运载火箭中的应用。
在攻坚克难中铸造一流发动机
“没有条件,我们就创造条件。”面对研制场地、设备能力均达到或者超过当时已有条件极限的情况,43所壳体技术负责人李瑞珍带领大家,拉开了一场挑战复合材料成型极限的“赛跑”。
研制期间,李瑞珍几乎每天都要去壳体生产现场。“壳体尺寸大幅增长,首要解决的就是芯模成型问题。”她说,原有的砂芯模重量大、挠度大,石膏芯模易开裂、产品表观质量差。
团队将目光聚焦到金属芯模上,10余种方案推翻重来,数百张图纸修改完善,最终应用镂空设计原理确定了金属芯模成型方案,保证了壳体顺利研制。
发动机研制生产完毕,即将接受最后一道考验地面试车,却遇到了一个棘手问题,如何突破吊车承载极限、吊高极限等,使之稳落于试验架?
这时,401所一室高永刚提出一个新想法,台体吊与汽车吊合力完成。然而,汽车吊工作路径为弧线、台体吊是“十”字,路径矛盾怎么解决、载重如何分配?当晚,团队立即投入推演路径设计、质心计算、支撑部位、吊具强度等工作中。
近200天里,他们经历了7次大型专家评审会,完成了重点承力部位的工装设计优化、强度和刚度校核,反复演练了起升高度、移动速率、各方位牵引力……
10月19日,伴随着巨大的振动与轰鸣,试验数据呈现出完美的测试曲线。而这成功的曲线,就是对团队人员辛勤付出最大的回报。
实习记者 李旭东
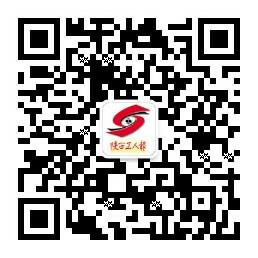
关注公众号,随时阅读陕西工人报